David's Diary: Wednesday, Sept. 12, 2001
Jeanneau Boat Factory
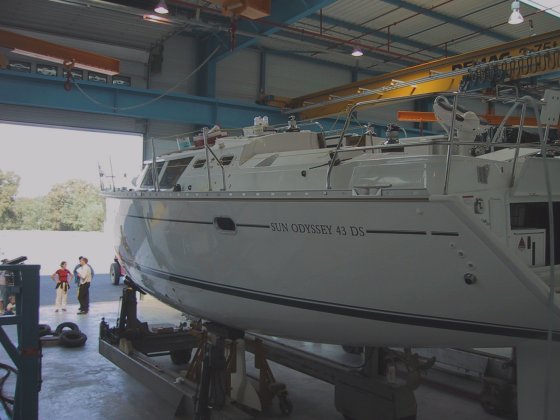
Dragonsinger
Today we got the first look at Dragonsinger, our new Jeanneau 43DS sailboat. After months of planning for this day we were up early for the long drive to Les Herbiers (355 kilometers one way). After stopping for lunch we arrived at the factory and were welcomed by Sophie Millaseau.
Les Herbiers is located South of Nantes in the middle of cornfields. We asked Sophie why one of the largest boat builders in the world has their factory located so far from the ocean. It turns out that Mr. Jeanneau, the founder of the company, was not a boat builder but a joiner. His hobby was racing very fast speedboats. He finally decided to build his own speedboat using his skills as a joiner. It just happened that the joinery was located in Les Herbiers. From this small beginning has come the Jeanneau company that we know today.
Sophie Millaseau
Sophie works in the customer service department. She has a degree in English and spent time in London teaching Grade 11 French. Sophie found that she did not have the patience for being a teacher so she returned to France where she joined Jeanneau.
In April 2001, Jeanneau opened a new state-of-the-art factory. Dragonsinger is being built in this factory. There are three separate buildings. The first is where the hull and deck are laid up in molds. The deck is actually made in two parts -- an outer and inner layer, which must be bonded together. A separate building is used to lay on teak decks (which we did not order).
Factory Line
The main building contains multiple factory lines. One line is dedicated to the 43DS. The hull enters the line at one end. Floors are raised to make it easier for workers to enter and leave the hull. It was remarkable to be able to look down and see wire runs, engines, through hulls, chain plates, and all of the other plumbing that makes a boat work, but which you normally never see.
The boat hull is mounted on a special cradle that has wheels. Each night, the floor is lifted and all of the hulls on the line are moved ahead one station. There are a total of five stations and the deck is only put on at the second last station. As the boat makes its way along the line more and more equipment is added. Many of the interior components are prefabricated. For example, the L-shaped galley comes complete is a single unit that is lowered into the hull and glued into place.
At the end of the line, the keel is added. As it happened today was the day that the keel was being put on Dragonsinger. Because of the difficult of the operation, the special glue used to seal the keel/hull joint, and the nature of moving the boat around we were not allowed onboard to see the inside of our finished boat. This was a disappointment as we have not seen an example of our forward two cabin arrangement and we had been really looking forward to seeing the reality. The good news is that in just a few short weeks we'll be seeing Dragonsinger in the water at Port St. Louis du Rhone in the South of France.
Testing Tank
After watching Dragonsinger be lifted out of the factory cradle and placed into a shipping one, we moved to the testing area. While the basic construction of Dragonsinger is finished there is still more than a week of testing and finishing work that needs to be completed. The factory contains an indoor tank large enough to hold four boats the size of Dragonsinger. After being built the sailboat is lowered into the tank. Here quality control technicians test all aspects of the boat, including onboard systems such as the engine. There is also a spray wash that helps to detect any possible deck leaks. Lists of manufacturing problems are created at this stage. Once the boat leaves the testing tank it is put into a holding area where any problems discovered during the testing phase are looked after. After testing our boat will be packaged up and shipped South.
We returned to the main administrative building where the children had a drink while Sophie took Karalee and I to the joinery. Jeanneau subcontracts many parts of their work (e.g., sails, spars, and cushions), but true to their roots they do all of their own joinery. The children were not allowed into the automated joinery, but Karalee and I were given a tour. Machines are used for sanding and varnishing teak veneer sheets and another for cutting out many of the parts. There is a separate varnish room for those parts that must be created by hand (those with curves or uneven surfaces).
A separate building holds wooden parts ready to be put into finished boats. Dragonsinger has hundreds of wooden parts and just before it was assembled a crate with all the parts needed to build the boat was created. We saw an individual section of the storage area that was dedicated to wooden parts for 43DS sailboats. Jeanneau have a large operation. From this location in the middle of the countryside, boats are shipped all over the world to happy owners like us.